In the ever-changing field of maritime engineering, few materials have made as significant an impact as aluminium. From the early days of small experimental boats to its role today in large commercial and defense vessels, aluminium has not only changed the industry but has also shaped it.
If you’ve ever searched for marine services near me or looked into opportunities with shipbuilding companies, you have likely seen the influence of aluminium in action. This article examines the history, evolution, and ongoing innovation in aluminium shipbuilding while covering everything from cruise ship building companies to mobile marine services and marine service engineers.
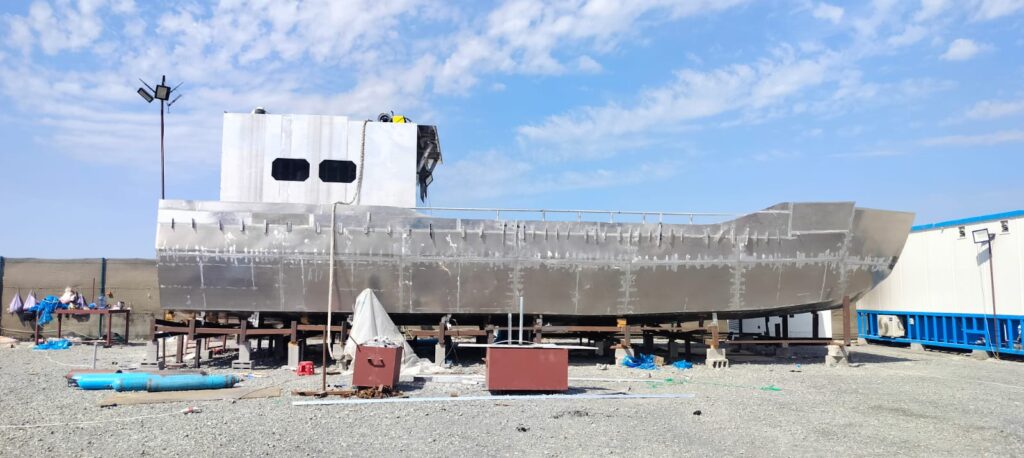
1. Early Beginnings (1891–1930s): The Spark That Lit the Way
1.1 The World’s First Aluminium Motorboat (1891)
The marine industry experienced a game-changing development when the first aluminium motorboat was launched in 1891. While steel was the main material, aluminium’s lightweight properties provided clear advantages in fuel efficiency and manoeuvrability.
1.2 Expansion and Initial Challenges
Despite its potential, the early 1900s brought challenges; aluminium was costly and not easily machinable. However, the success of small-scale applications motivated aluminium boat builders to continue innovating.
1.3 Technological Advances in the 1930s
The 1930s introduced important technologies like better sheet metal forming and early welding methods. These improvements led to stronger joints and enabled the use of aluminium in larger, more complex vessels.
1.4 A Material Rises in Maritime Engineering
During this time, aluminium gained recognition not just in commercial vessels but also in military and recreational boats. This marked the start of a trend that would later influence major shipbuilding companies worldwide.
2. Mid-20th Century Developments (1940s–1960s): The Material of the Future
2.1 Introduction of Aluminium-Magnesium Alloys
In the 1940s, the introduction of aluminium-magnesium alloys enhanced the strength and corrosion resistance of marine components. These alloys were essential during WWII, allowing for faster, lighter, and more agile military vessels.
2.2 TIG Welding in the 1950s: A Breakthrough Moment
The adoption of Tungsten Inert Gas (TIG) welding marked a significant turning point. This method enabled ship building companies to produce aluminium vessels on a larger scale while ensuring high precision and quality.
2.3 The 1960s: Birth of Marine-Grade Aluminium
By the 1960s, marine-grade aluminium became widely accessible. Its resistance to saltwater corrosion made it the preferred material for many ship building companies in the USA, aluminium boat builders, and marine service providers.
3. Expansion and Diversification (1970s–1980s): Aluminium Goes Big
3.1 Strategic Shift to Aluminium Construction
During this time, many American ship building companies and firms across Europe and the Middle East started to shift from steel to aluminium. It offered lower maintenance costs and a longer service life, which were key advantages for commercial fleets.
3.2 The Benefits of Aluminium in Marine Applications
• Lightweight structure → better fuel efficiency
• High resistance to corrosion → ideal for coastal and oceanic vessels
• High strength-to-weight ratio → suitable for fast ferries and patrol boats
These benefits solidified aluminium’s position as a favoured material for both shipbuilding companies in the UAE and mobile marine service providers.
3.3 Scaling Up: Aluminium in Larger Maritime Vessels
By the late 1980s, aluminium was no longer restricted to small crafts. Cruise ship building companies began experimenting with hybrid hulls that incorporated aluminium superstructures to lower top weight and enhance balance.
3.4 Leisure Boating and Racing
This period also saw a surge in recreational marine services. Aluminium boats were easy to transport, repair, and customize, making them very popular for fishing, racing, and yachting enthusiasts.
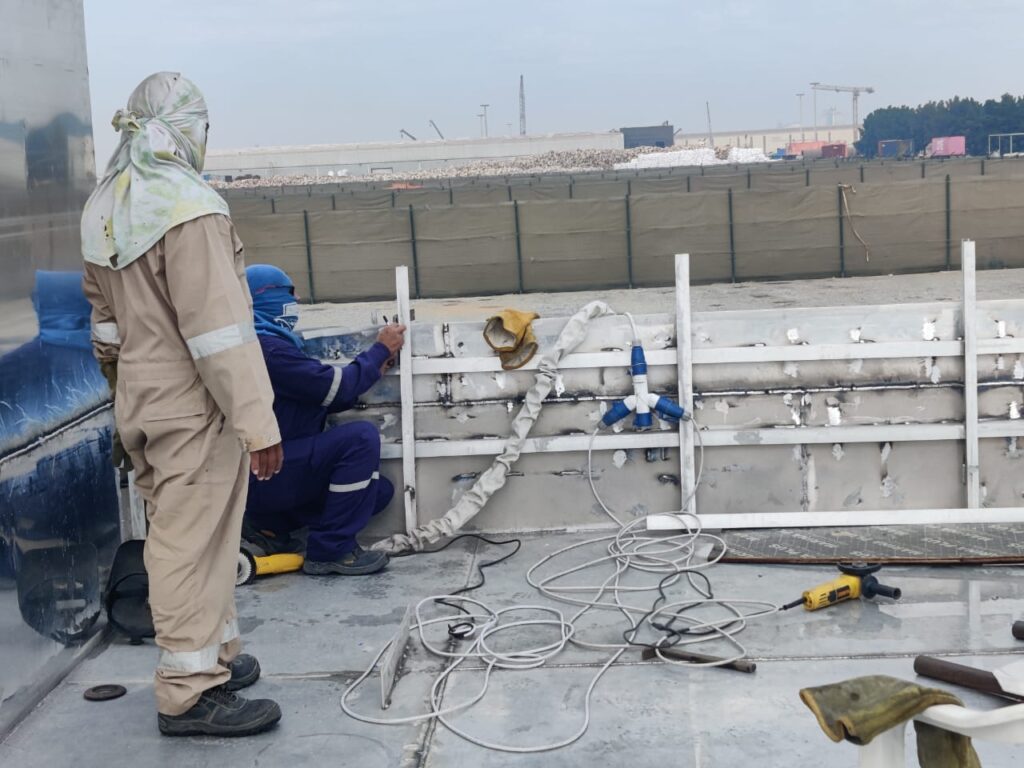
4. The Modern Era (1990s–Today): Smart Ships, Smart Materials
4.1 Smart Materials for a Smarter Industry
Today’s top ship building companies utilize AI-driven design and CNC machining to improve performance. Aluminium remains central to these developments due to its compatibility with modern technologies and sustainability goals.
4.2 Sustainability & Recyclability in Shipbuilding
As global marine industries move toward sustainable solutions, aluminium stands out for its high recyclability and low lifecycle emissions. It plays a crucial role in making marine operations more environmentally friendly.
Marine service providers now focus on eco-friendly repairs and retrofitting; aluminium helps them meet those standards while extending vessel lifespan.
4.3 UAE’s Rise as a Shipbuilding Hub
The UAE has emerged as a leader in marine engineering, with many ship building companies in the UAE offering cutting-edge technology and top-quality marine services.
4.4 Careers in Modern Shipbuilding
Aluminium’s ongoing dominance has led to a surge in demand for skilled workers. Positions like marine service engineer are becoming increasingly specialized and offer great job potential for those entering the marine sector today. If you’re considering a shipbuilding career, now is a great time to act.
Conclusion: Aluminium is Steering the Future
From humble beginnings to powering major shipbuilding companies worldwide, aluminium has proven to be a foundation of innovation in marine engineering. Its flexibility has led to its use in everything from personal watercraft to naval destroyers.
Whether you’re a marine enthusiast, a business decision-maker, or just someone looking for “marine service near me,” aluminium-built vessels are likely central to what you’re searching for.
If you’re seeking trusted, efficient, and future-forward marine solutions —
Explore VU Marine, one of the top shipbuilding companies delivering world-class performance right from the heart of the UAE.